Operational excellence is more than a buzzword.
It’s a key ingredient to your company’s success.
Operational excellence is when your business functions at its best every day. It happens when you remove inefficiencies, and create a culture of continuous improvement.
But how does it work, and how can you practice it in your business?
First, let’s discuss what operational excellence is and identify tips on how to apply it to your business.
What does operational excellence mean?
Operational excellence means running a business in the best way possible to achieve desired outcomes. Dr. Joseph M. Juran introduced this term while teaching Japanese business leaders how to improve quality.
While it may seem simple, operational excellence depends on the entire business. Think of it as a tuned engine, with processes, tools and people, working in harmony to move the business forward.
It's also a mindset in the work culture that inspires everyone to keep getting better.
Operational excellence vs continuous improvement
When we talk about operational excellence, we often hear the term continuous improvement. While the two are symbiotic, they’re different. While the two are symbiotic, they’re different.
Operational excellence is when a company has long-term and sustainable growth by running things well. This includes improving processes, reducing waste, and delivering value to customers.
Continuous improvement is a strategy used by companies to achieve operational excellence. It means making things better over time by constantly looking for ways to improve.
Why does operational excellence matter?
So what advantages can you reap by achieving operational excellence?
As Vinod Srinivasa, OPEX professional at Bank of America, puts it, “Operational excellence is the thread that unifies an organization’s functions and channels them to enhance efficiency in every aspect.”
![]() |
But how does operational excellence help your business achieve higher productivity and growth? Let’s get into the nitty-gritty.
Cost savings
The main ideas behind operational excellence is reducing inefficient and wasteful business processes. By doing so, you reduce cost caused by errors and optimize your resources, which leads to significant cost savings.
Improved customer experience
An Emplifi report shows that 86% of consumers will leave a brand they initially trusted after only two poor customer experiences. Operational excellence acts as a foundation for building strong and loyal customer relationships.
Operational excellence drives your business to deliver quality products or services that meet and exceed customer expectations. Thus, driving revenue and long term growth.
Increased agility and competitiveness
Competing in today’s business landscape is challenging. That’s why operational excellence gives you an upper hand. By maximizing productivity, efficiency, and adaptability, you gain the upper hand to thrive amid changing market dynamics and customer demands.
A flourishing company culture
One of the most underestimated aspects of a successful business is company culture. A global culture survey found that 72% of employees agree that culture drives change at work.
An operational excellence program does two things. First, it creates a culture of improvement. Second, it solves employee pain points. When these two things happen, you get a positive work environment. This environment encourages collaboration among employees, improves engagement and attracts top talent.
Top 4 operational excellence methodologies
There are many ways for implementing operational excellence. We’ve compiled the top four to help you optimize your business operations.
1. Lean manufacturing
Lean manufacturing is one of the main methodologies used to achieve operational excellence. In fact, the methodologies mentioned below all fall under its umbrella.
Lean manufacturing centers around cutting waste in production processes. The goal is to increase efficiency and reduce operating costs. In each step of the process, you find ways to cut unnecessary steps, reduce inventory or hire better talent.
Lean manufacturing also highlights unnecessary steps, delays, and inefficiencies. This way your team can make improvements and streamline its operations.
![]() |
One popular technique of lean manufacturing is the Kanban system, a visual to-do list for managing work. Kanban shows you the status of your work at a glance and prevents you from taking on too much at once.
Lean principles empower businesses to deliver quality products in the most efficient way.
2. The Shingo model
The Shingo model is like a state of mind.
It’s a set of principles developed by Japanese industrial designer Shigeo Shingo. It emphasize the alignment of company systems, principles, and behaviors.
The Shingo model fosters a culture of excellence by encouraging continuous improvement and waste reduction. The main focus is to create value for customers, and establish strong leadership and cultural frameworks.
![]() |
The main Shingo guiding principles are as follows:
- Respect Every Individual
- Lead with Humility
- Seek Perfection
- Embrace Scientific Thinking
- Focus on Process
- Assure Quality at the Source
- Improve Flow & Pull
- Think Systemically
- Create Constancy of Purpose
- Create Value for the Customer
With the Shingo model in place, everyone is committed to continuous improvement and innovation, and delivering quality products or service
3. Six Sigma
Numbers don't lie. So, many businesses are looking for a data-driven approach to improve their processes.
Six Sigma is a data-driven approach that aims to reduce defects and improve quality by eliminating variations. The goal is to achieve 3.4 defects per million opportunities. In achieving that, you can improve customer satisfaction, reduce costs, and increase efficiency.
![]() |
Six Sigma was originally coined by Motorola in the 1980s but has since been adopted by many global organizations. It follows a structured approach called Define, Measure, Analyze, Improve, and Control (DMAIC).
Six Sigma uses the power of data to minimize defects and achieve superior quality standards., giving you a competitive edge.
4. Kaizen
Kaizen is a direct subset of lean manufacturing that stresses incremental change to achieve better results over time.
The main idea of Kaizen is that over time, even small, continuous improvements can have a significant impact. It encourages employees to identify opportunities for improvement, suggest ideas, and implement changes.
![]() |
Kaizen empowers employees at all levels to contribute to improvement. Your workforce will learn, adapt, and innovate, paving the way for operational excellence.
5 tips for achieving operational excellence in your company
1. Pick a methodology that matches your needs
Operational excellence has become the Holy Grail for modern businesses. Over 65% of companies have an annual OPEX budget of up to US$1 million, according to the PEX Network’s 2023 PEX Report.
But there’s no one-size-fits-all approach to achieving operational excellence. So to compete, you need to choose a methodology that matches your business strategy and goals.
Manufacturing companies tend to choose lean manufacturing or Six Sigma to cut waste and ensure quality. The service industry often uses the Shingo model or Kaizen to improve service delivery, optimize workflows, and improve customer satisfaction.
2. Make things measurable and repeatable
It’s not enough to simply make changes — you need to ensure those changes last for the long haul. That’s where making them measurable and repeatable comes into play.
Measure and track the progress of your changes by establishing metrics and key performance indicators (KPIs). KPIs make it easier to determine what works and what doesn’t.
Creating standard operating procedures (SOPs) to document and make new processes repeatable is also key to sustainable improvement. It's as if you’re building a playbook that everyone can refer to so that the new processes become ingrained in your business’s DNA.
3. Involve your employees as much as possible
According to a BTOES insight report, 53.1% of organizations believe that their top challenge for reaching operational excellence is changing and improving company culture.
![]() |
To overcome this hurdle, build a culture that embraces operational excellence by empowering employees, fostering collaboration, and clear communication.
Since your employees are the ones following company processes, have them join in when making changes. This way, those changes will work for those on the floor. Encouraging communication and feedback will also help your employees share their ideas, address and resolve problems, and drive innovation.
4. Always communicate
Always, always, always communicate.
In the same BTOES report, 36% of organizations said executing and sustaining improvements was a challenge to achieving operational excellence.
So, when new policies are added or changes are made, managers need to communicate with everyone to make sure the entire business is aligned. Send reminders or plan meetings to help set your employees up for success.
5. Automation is key
The secret shortcut to operational excellence is automation. Automation tools help you do work more efficiently, so you can do the most important tasks to achieve business excellence.
Motion’s AI project management tool takes care of tedious scheduling, recurring tasks, and work delegations in one place, freeing you up for what matters the most.
Take Sparkmate, a tech startup, for example. Its founder, Morgan Pelissier, used Motion to automate everything he had to do. Motion handled weekly planning, delegating work, prioritizing tasks, and shipping projects. As a result, Sparkmate completed work faster, worked better, and got closer to achieving its goal of operational excellence.
Motion streamlines your workflow to drive operational excellence
Ready to take your business to the next level of operational excellence? Motion has your back.
With Motion, you can simplify your workflow, get things done quickly, and perform at your best.
We make the hard things easy with automation and empower you to focus on what's important in business. So say goodbye to inefficiencies, and welcome a new era of productivity and success.
Get started today with Motion.
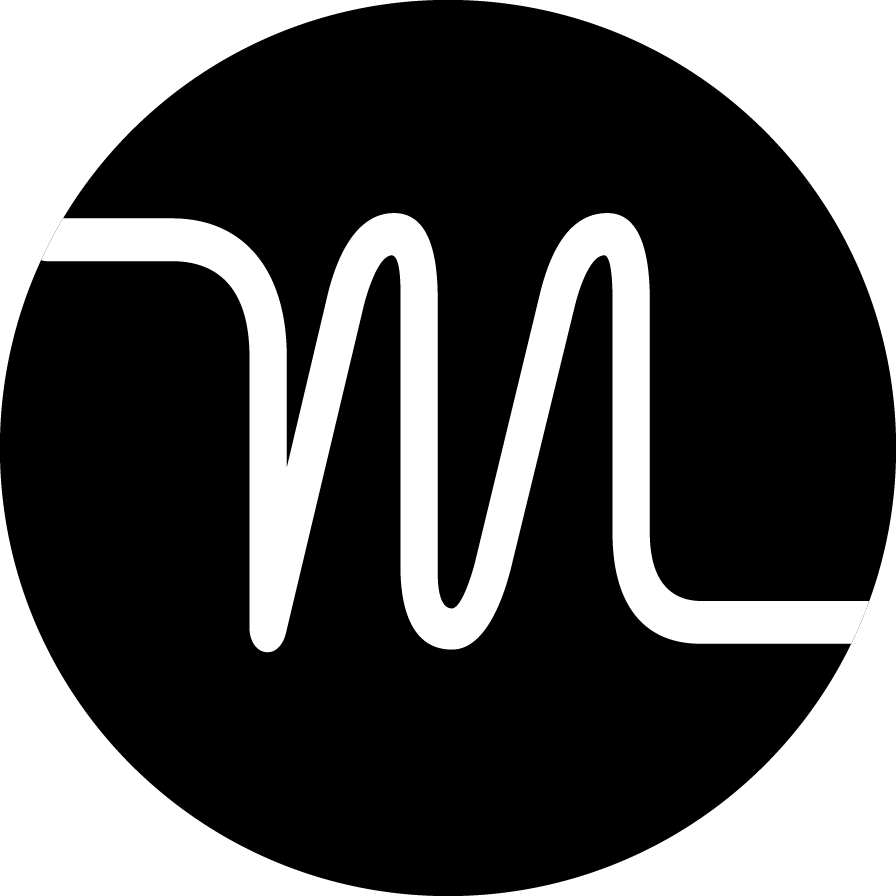