Let’s pause for a moment and consider the idea of project success. As a business owner or project manager, what is it that makes a project successful for you?
The standard answer is on time and within budget. But in a world where project management tools are so freely available, that’s no longer enough. It used to be that a huge percentage of projects failed, but that’s a stat that’s coming down all the time. The extra bit that defines a project’s success is the quality of its outcome.
That supposes that you can measure quality. And sometimes you can. If you’re setting up a manufacturing production system, you can measure the quality of the products that roll off the line. You can do that by measurement or chemical analysis.
But how do you assess the quality of your project when the outcome can't be easily measured or analyzed? That's where project quality management (PQM) can help you. In this article, you'll learn how to define, monitor, and manage project quality, and about many of the tools you can use to assess the quality requirements of your projects.
How do you define project quality?
How do you measure the quality of your projects? Many project managers will turn to the bible of project management: Project Management Institute’s Project Management Body of Knowledge (PMBOK).
Going way back to at least the Fourth Edition (2008), PMBOK consistently defines quality as “the degree to which a set of inherent characteristics fulfill requirements.” Or, in everyday language, the project outcome does what it was meant to do.
But something’s missing. Perception. As the business owner or project manager, you might look at a project outcome and be 100% happy with it. But someone else might look at it with a more critical eye, pointing out the flaws.
And when that second person is your customer or another important stakeholder, that changes things. A lot.
The 3 phases of a project quality management plan
Even if you thought about quality standards before your project began, your customer or stakeholder may still have a different perception. That is, unless you worked with them to create a project quality management plan (PQMP).
That'd establish quality planning, quality control, and quality assurance procedures for your project. It helps you maintain high-quality standards over the entire project lifecycle.
![]() |
Quality planning
This is the most important step in creating a PQMP. If you don't define upfront what the quality requirements are for this project, you're opening yourself to a world of pain later. You must engage with your stakeholders to agree on what quality would look like at the end of your project, and what processes you will use to manage that. And you must carefully document these.
This plan will be the reference you’ll use during the project, and return to at project close when you want to tick the quality box. So, as far as possible, you need to be specific and include metrics for measuring quality during and after the project. You might even create a quality checklist to complete along the way.
Quality assurance
This step is about assuring stakeholders that project quality is being maintained as defined and promised. In a sense, it's more about managing stakeholder expectations and avoiding unwelcome surprises down the line.
Quality assurance happens on two levels: the products and services you’re delivering and the project itself. You need to look at it from both perspectives. Practically, your project team will go through a checklist or conduct a project audit.
Quality control
When you’ve agreed with stakeholders on the definition of quality for your project, you’re ready to go operational. This is the phase where you step into a monitoring role, checking the quality of work as completed and at a more granular level.
It usually will involve testing. You must be sure each deliverable’s “inherent characteristics” satisfy the requirements determined during planning. The goal is to ensure that rules are followed and the expected quality standards for deliverables are met throughout the project.
What makes a good project quality plan?
If you consult the PMBOK Guide, Sixth Edition, you’ll discover that a good PQMP must contain certain things:
- Specific quality standards for your project outcomes
- The agreed quality objectives of your project
- Roles and responsibilities of all involved in the PQMP
- A list of project deliverables and processes that are subject to quality review
- Details of quality management activities planned for your project
- Identification of quality management tools to be used for your project
- Details of quality management procedures or processes on your project.
In Agile projects, quality management is largely accomplished using the Definition of Done. As the words suggest, it sets the rules that determine when a task or feature has been completed and is ready for delivery.
![]() |
Benefits of PQM
The most obvious advantage of PQM is that it helps you to make sure that your products or services are of high quality. But there are also several benefits to setting up and maintaining a solid PQM process for all your projects.
Customer satisfaction
Without customers, there is no business, so keeping them satisfied with the quality of what you provide is critical to sustaining your business. But it’s not just your products or services on display. Even if a deliverable ticks all the quality boxes but the process of producing it wasn’t happy, you have a problem.
It’s as much about producing quality products or services as it is about managing your customers' expectations.
Better quality products and services
We touched on this benefit already, but it’s worth digging a little deeper. As a business person or a project manager, no one needs to tell you that the foundation of your business is the products or services you provide. Your success as a going concern depends on them.
PQM is a critical tool in the quest to improve your internal processes and ensure that the quality of your deliverables meets or surpasses customer expectations.
Increased productivity
This is something that's often misunderstood. Productivity involves a lot more than just working fast and efficiently. Most teams these days are multidisciplinary. Tasks are passed from one team member to the next, for each to apply their specialist skills.
If you have implemented a PQM system, every team member will always be clear on what they need to do and by when. That relies on better communication, which strengthens relationships within your team. It also tightens internal processes and reduces rework – which leads to better productivity and continuous improvement.
Financial growth
When running a project, your goal will always be to deliver a quality product or service without breaking the bank. That can be hard without a PQM system, which provides the planning, assurance, and control to tackle problems before they eat your budget.
And if you use PQM to tighten your processes and improve productivity constantly, you can generate higher profits. And better profit margins will usually translate to financial growth.
Enhanced project performance
The entire point of PQM is to ensure your project is executed efficiently and effectively. As a result, your project team produces better work, leading to a higher quality outcome.
Happily, this also reduces the risk of having to redo work, limits delays in the project, and helps you manage your project budget.
Better resource utilization
Greater efficiency and effectiveness on your project means you’re using your resources more productively. PQM gives you a framework to better monitor, control, and manage how your team uses the resources it has.
That helps your quality management drive because you’re using your time, money, and people better. It also improves productivity and prevents project team members from being overburdened by excessive workloads.
Increased stakeholder confidence
One of the trickiest elements of project management is to keep your important stakeholders in the loop and in a positive state of mind. These people have a stake or an interest in your project because it’ll affect them somehow.
And if you have a PQM system in place, it automatically increases the confidence stakeholders will have in the quality of your project. And that could get their support on future projects.
Prevention over inspection
To be clear, producing quality products or services is costly. But the cost is always higher if work has to be redone or your business suffers reputational damage. Effective PQM will help you make sure that the cost of quality is controlled.
As your doctor will likely say, prevention is better than cure. It’s the same with projects. PQM is a way you can prevent quality problems from causing your project to fail or deliver poor results.
Continuous improvement
This technique came to prominence after being observed in Japanese factories, from which it was exported to the rest of the world in various forms. It’s based on a simple principle: small incremental process improvements over time.
It applies equally in projects where small changes to how your team works can impact project success. Of course, it does require the awareness that PQM gives you of the issues. And you must be determined to use those lessons on future projects.
![]() |
Where the rubber meets the road
When it comes to PQM, there is no shortage of ways to implement it. With so many techniques in play, you're free to experiment until you find the ones that work for you. But always be careful to keep your options open.
Not every tool will work in every situation, and you may find that a range of devices works best for you. Factors you should consider when making your selections include your industry and your team's preferred ways of working. Some of the tools and techniques you might use:
- Network diagrams let you map out project tasks and deliverables visually. They help you identify which tasks depend on others and reveal the critical path of your project.
- Affinity diagrams are useful for exposing connections between separate data points. They're also very useful in brainstorming sessions.
- Matrix diagrams help you visualize both the relationships between data points and the strength of those relationships. Different matrix shapes are used, depending on how many items or groups of items you want to analyze.
- Process decision program charts are a predictive tool. They help you determine what could go wrong and help you plan for different scenarios.
- Interrelationship diagrams show cause-and-effect relationships affecting project outcome quality.
- Prioritization matrices help you identify and prioritize issues that may arise during PQM
- Cost of Quality (COQ) analysis calculates the financial impact of resources you apply to achieve quality.
- Statistical process control is a set of analytical methods to monitor and control a process, to ensure it operates within required limits.
- Control charts let you see visually how a manufacturing or business process behaves over time.
- Pareto charts are graphical representations of the frequency of defects, costs, time, and other production factors.
- Flowcharts or process diagrams can help you identify potential bottlenecks or areas for improvement.
- Cause-and-effect diagrams can help you identify the actual cause of a particular issue.
- Histograms help analyze the frequency of occurrence in intervals or ranges to show production output, supplier performance, and other measurable items.
- Run charts are useful for spotting data trends or patterns over time, particularly before-and-after comparisons.
- Scatter diagrams help you analyze the relationships between variables and identify any correlations between them.
![]() |
Leveraging Motion to manage project quality
Determining what is or isn’t a quality outcome can be subjective. Without quantitative data, it’ll depend on who’s making the assessment and their frame of reference. It may even depend on their mood and relationship with you – the business owner or project manager.
The best you can do is to preempt adverse outcomes by practicing effective and proactive stakeholder management. Catching a mistake early allows you to intervene quickly and take immediate corrective action. And that always plays well with stakeholders.
To know how your projects are progressing, Motion can help you track project progress in a way that keeps you up to speed on what everyone is doing and lets you spot deviations from the planned schedule or scope.
Based on your priorities, deadlines, dependencies, and available time, Motion produces optimal intelligent calendars so you and your teams work on the right things at the right time.
Check it out today by registering for Motion’s 7-day free trial.
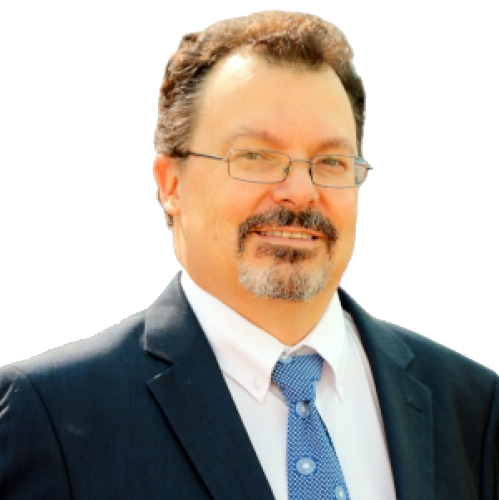
After 40-odd years of working in technology, project management, media, and marketing, Brian's career and growth journey has exposed him to a wide range of niches. He brings this breadth of knowledge and expertise in his content work through enriched storytelling and original concepts that make SaaS content engaging and accessible for readers of all stripes.